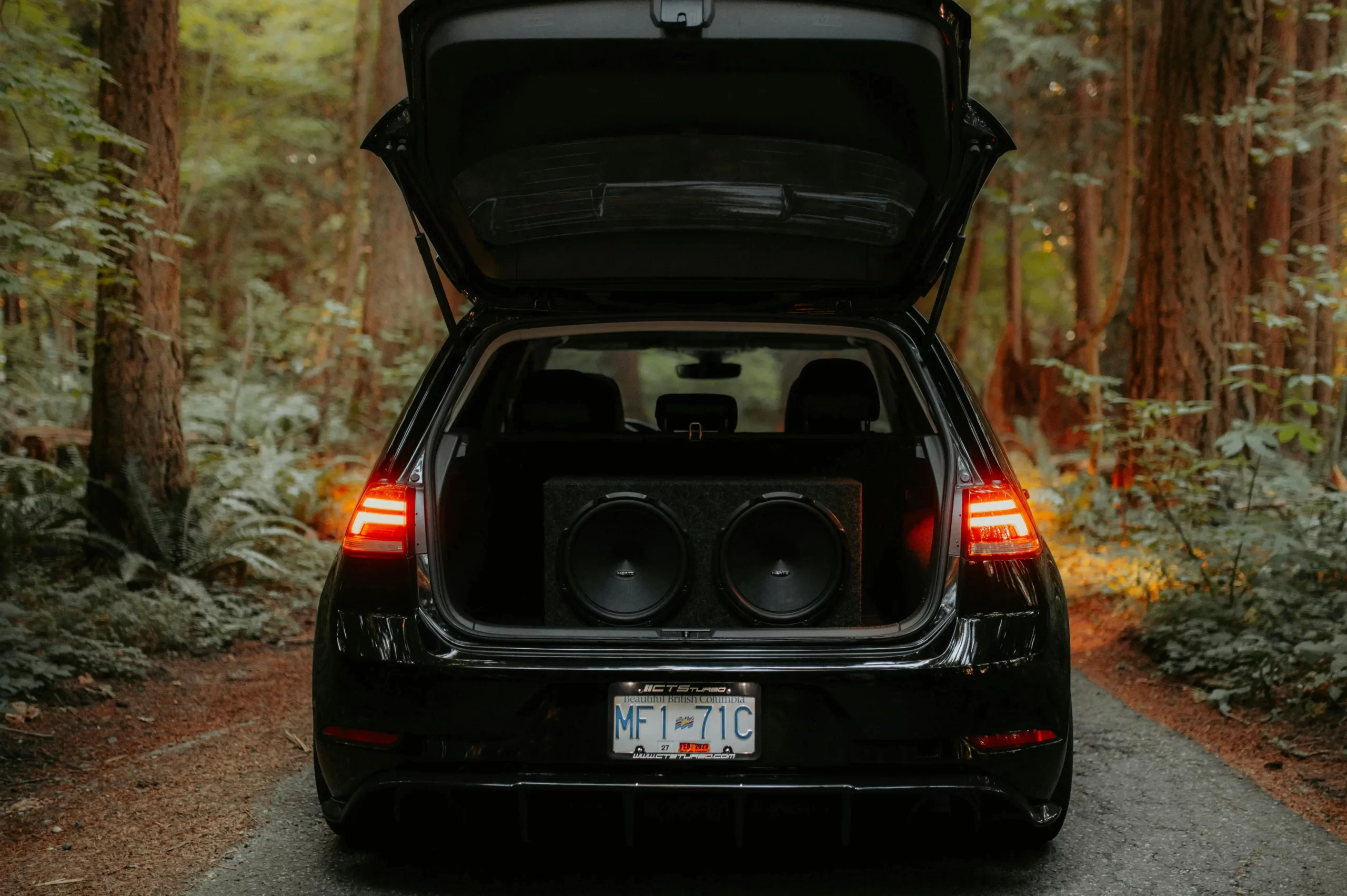
Installing an aftermarket sound system can totally transform your driving experience — giving you better sound clarity, deeper bass, and more control over your car’s audio environment.
But without proper care, adding aftermarket electronics can introduce a new risk: electrical corrosion.
Corroded wires, terminals, and connectors can lead to serious problems like speaker failure, amplifier shutdowns, parasitic battery drain, or even electrical fires. The good news? With a few smart strategies, you can easily prevent electrical corrosion in your car’s sound system and keep it running strong for years.
Here’s exactly how to do it.
What Causes Electrical Corrosion in Car Audio Systems?
Before we jump into prevention tips, it’s important to understand what you’re up against.
Electrical corrosion happens when moisture, oxygen, and electricity combine to attack metal parts. In cars — especially those with aftermarket installations — this can happen more easily due to:
- Poor quality wiring or connectors
- Improper installation (e.g., exposed wires)
- High humidity or water leaks inside the car
- Salt exposure (especially in winter climates)
- Battery acid vapors under the hood
Once corrosion starts, it creates high resistance points, poor conductivity, and eventually component failure.
Signs of Electrical Corrosion in Car Audio Systems
Here’s what you should watch for:
- Crackling, distorted, or weak audio
- Sudden speaker or amplifier shutdowns
- Frequent blown fuses
- Visible green or white powder on wires or terminals
- Unexplained battery drain
Catching corrosion early is key to avoiding major headaches later.
Best Practices to Prevent Electrical Corrosion
Now, let’s get into how to prevent corrosion when upgrading or maintaining your car’s sound system.
1. Use High-Quality Wires and Connectors
Not all wiring is created equal. Always invest in:
- Oxygen-Free Copper (OFC) wire (not cheap Copper-Clad Aluminum or CCA)
- Gold-plated terminals and connectors (gold resists corrosion much better than bare metal)
- Heat-shrinkable terminals for better moisture resistance
Better components cost more upfront, but they can save you thousands in repairs later.
2. Properly Solder and Protect Connections
Wherever possible:
- Solder your wire connections instead of just twisting them together.
- After soldering, use heat shrink tubing to seal the joint completely.
- For non-soldered connections, use dielectric grease inside connectors to repel moisture and prevent corrosion.
Pro Tip: Never leave any exposed copper showing at the end of a wire — moisture will attack it first.
3. Seal Entry Points
When running wires from inside the cabin to the engine bay (e.g., for amplifiers):
- Use grommets to protect wires passing through metal panels.
- Seal any unused holes with silicone sealant to prevent water intrusion.
Water leaking into the cabin or trunk is one of the fastest ways to cause widespread corrosion.
4. Keep Amplifiers and Crossovers Elevated and Ventilated
If you install amplifiers or crossovers in the trunk:
- Mount them above floor level — not directly on carpet or metal, where condensation can collect.
- Allow good airflow to prevent heat buildup, which can accelerate chemical reactions (including corrosion).
5. Regularly Inspect and Maintain
At least twice a year:
- Inspect battery terminals, ground wires, amp connections, and speaker wiring.
- Look for signs of corrosion, loose fittings, or moisture accumulation.
- Clean battery terminals with a wire brush and apply a protective spray or dielectric grease.
Early maintenance can spot small problems before they cause expensive repairs.
6. Mind Your Ground Connections
Poor grounding is a top cause of corrosion and electrical problems:
- Always ground your amplifier and audio components to bare, clean metal, not to painted surfaces.
- Keep ground wires as short as possible — ideally under 18 inches.
- Use star washers to bite through paint and ensure a solid connection.
A bad ground creates resistance, which generates heat and promotes corrosion even faster.
7. Protect Your Battery and Charging System
Aftermarket systems place extra load on your electrical system. An overloaded battery can vent acidic vapors, which cause corrosion throughout the engine bay.
To prevent this:
- Make sure your battery and alternator are properly sized for your sound system.
- Consider installing a battery isolator or second battery for large systems (1000W+).
- Keep your battery terminals clean and coated with a protective anti-corrosion gel.
Bonus Tip: Install a Moisture Barrier
If you live in a humid climate or near the ocean, it’s worth going the extra mile:
- Use moisture-absorbing packets inside enclosed spaces (like amp boxes or under seats).
- Install vapor barriers behind door panels after speaker upgrades.
It’s a small investment that can add years of life to your setup.
Final Thoughts
Installing an aftermarket sound system is a fun and rewarding upgrade — but it comes with new responsibilities. Electrical corrosion can silently destroy your system if you’re not careful.
By using high-quality parts, sealing and protecting connections, maintaining your wiring, and watching for early signs of trouble, you can enjoy crystal-clear sound for years without unexpected breakdowns.
Don’t let corrosion ruin your ride — protect your investment from Day One!
Leave a Reply